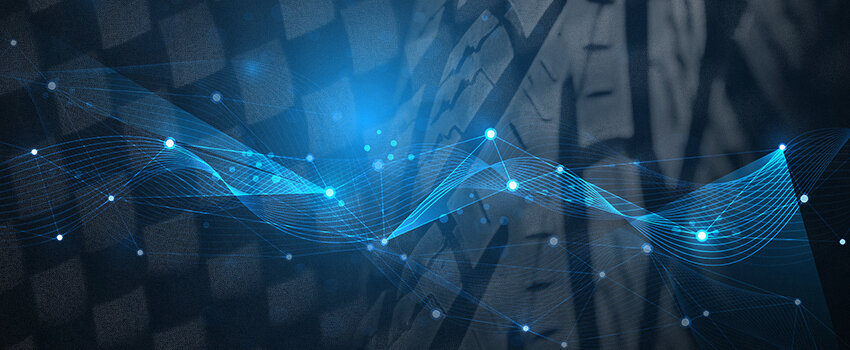
Interplanetary Technology
This NASA Glenn innovation comprises a non-pneumatic, compliant tire utilizing shape memory alloys (mainly NiTinol + derivatives) as load bearing components. These shape memory alloys are capable of undergoing phase transitions at the molecular level with significant reversible strain (up to 10%), an order of magnitude more than ordinary materials, before undergoing permanent deformation. Commonly used elastic-plastic materials (e.g. spring steels, composites, etc.) can only be subjected to strains on the order of ~0.3-0.5% before suffering plastic deformation. Hence, the use of a NiTi shape memory alloy produces a superelastic tire that is elastic like rubber, yet strong like titanium.
The utilization of shape memory alloys provides enhanced control over the effective stiffness as a function of the deformation, providing increased design versatility. For instance, the tire can be made to soften with increased deflection, reducing the amount of energy transferred to the vehicle during high deformation events. In addition, the use of shape memory alloys in the form of radial stiffeners, as opposed to springs, provides even more load carrying potential and improved design flexibility.
Check out our feature, alongside NASA, on the popular YouTube science channel, Veritasium, showcasing our work with shape memory alloys for tire applications.
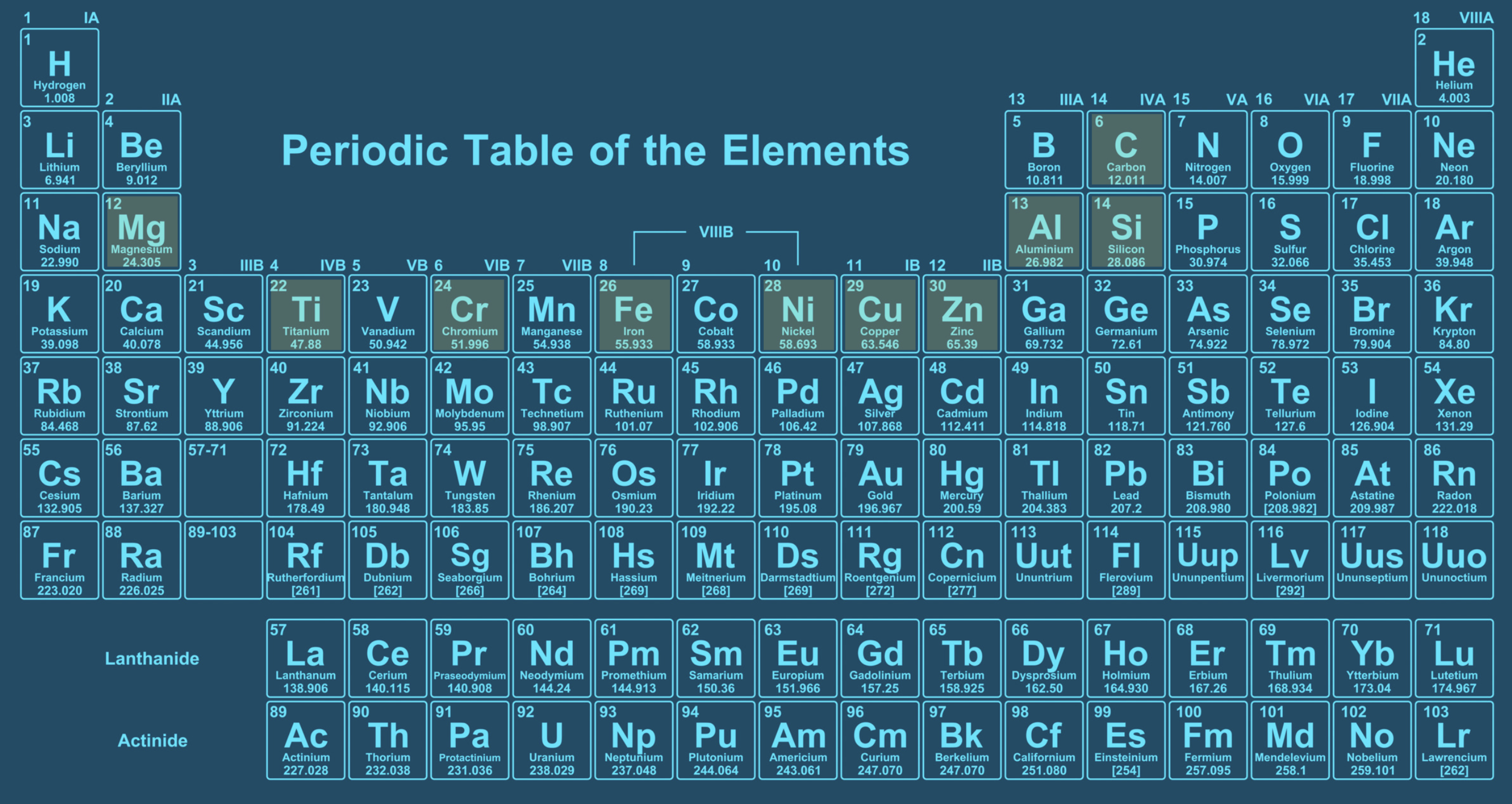
Shape Memory Alloys: a superelastic material
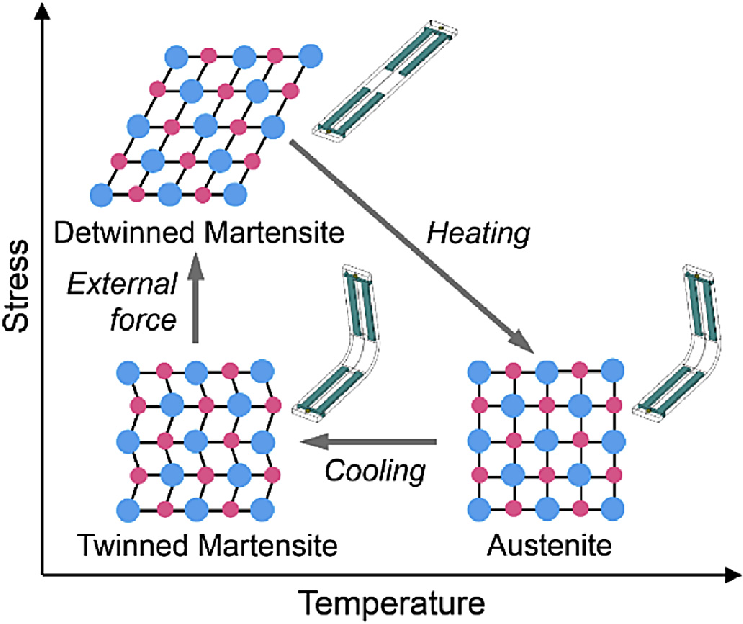
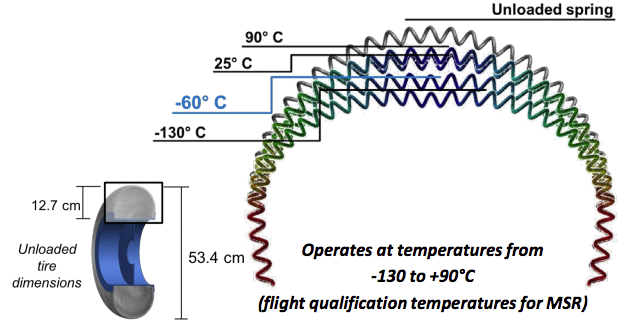
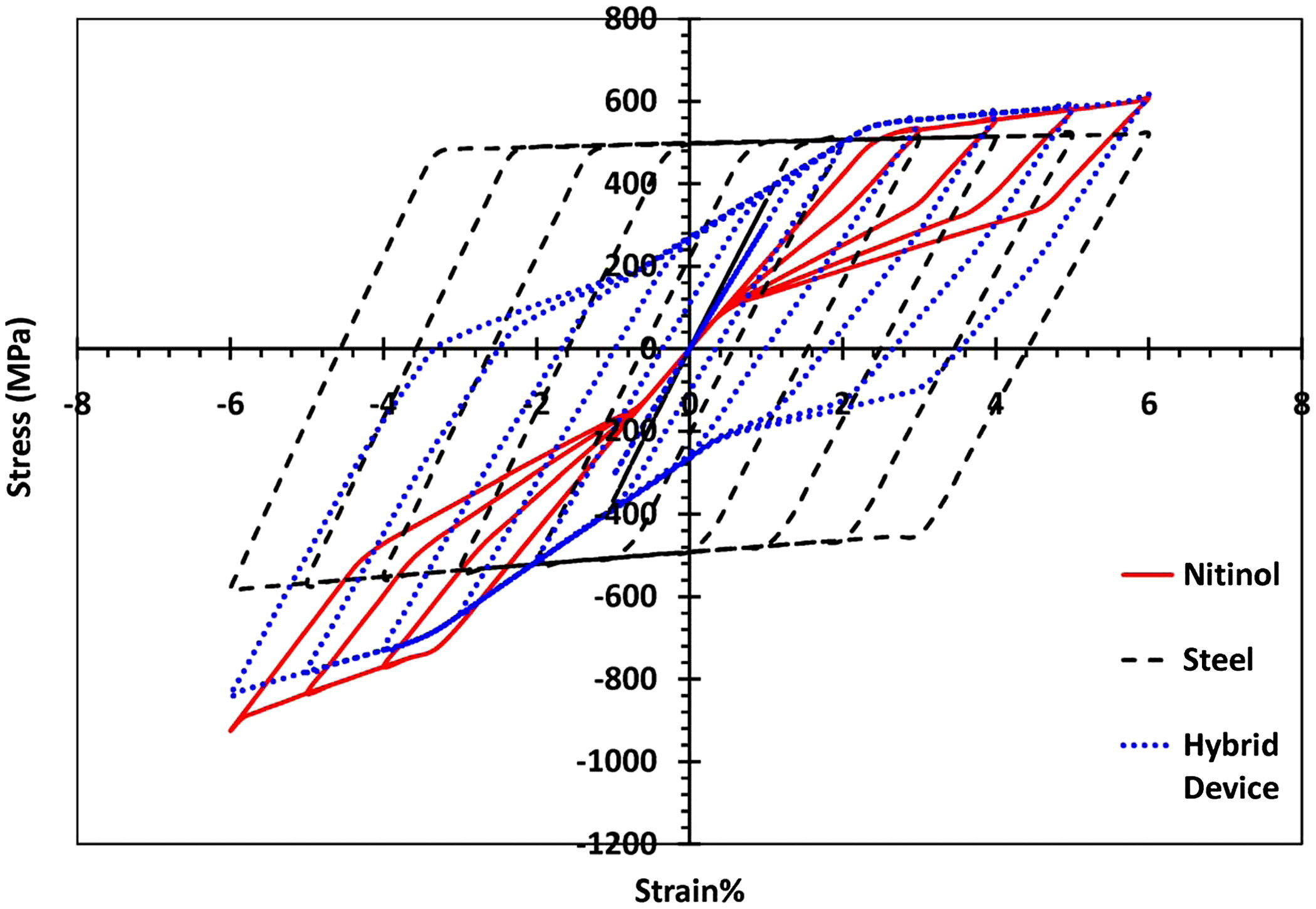
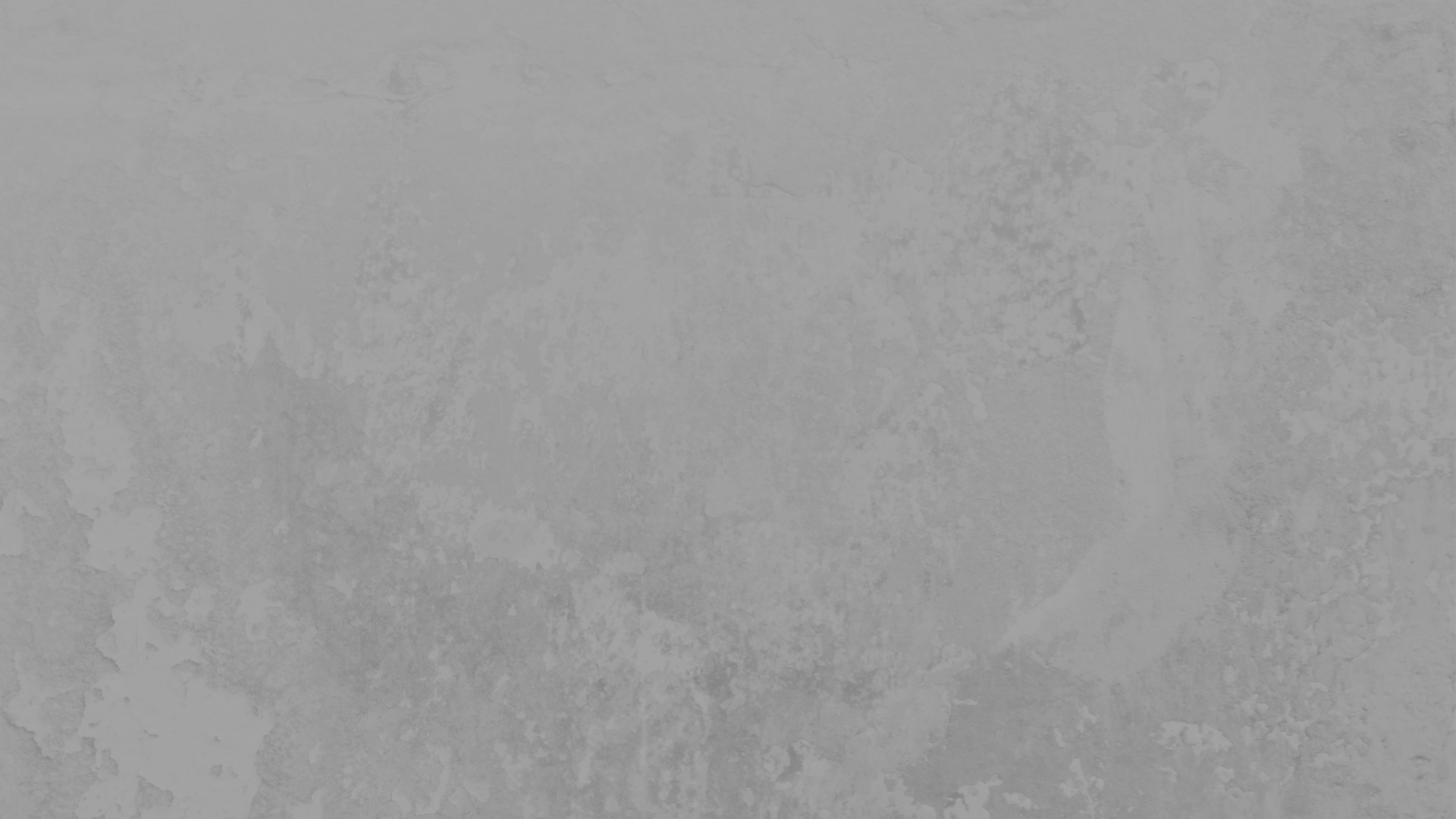
Designing with SMAs
Shape memory alloys (SMAs) display a “superelastic”, stretchy and bouncy effect when they are deformed above their specific transformation temperature. Above this transformation temperature, the material is in an austenitic phase. When stress is applied, the deformation causes a stress-induced phase transformation from austenite to deformed martensite. When the applied stress is removed, the material immediately springs back, and the crystal form returns to the austenite phase. This process of stress-induced phase transitions is what powers the incredible properties of an alloy such as NiTinol (Nickel Titanium).
As an actuator, SMAs get their name from their unique ability to deform and then regain their original shape when they are heated or cooled beyond a specific temperature range. Similar to stress-induced transformations, the application of heat can trigger a phase transition in which the underlying crystal structure reorganizes itself and “remembers” its previous shape. This process is so powerful, it has been harnessed as a rock splitting technology and utilized in critical automotive and aerospace actuator components.
S M A R T . T I R E S
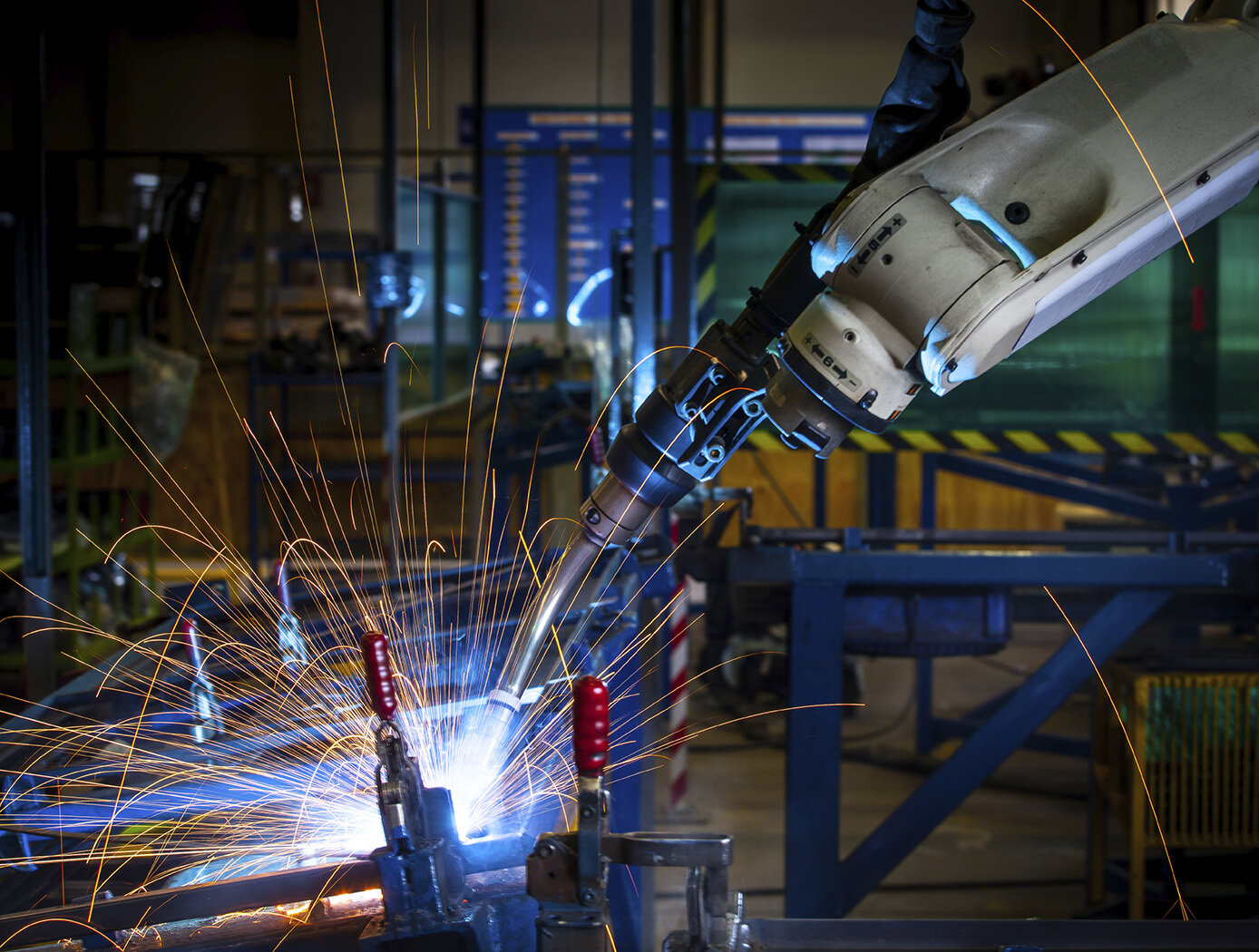